Arai helmets are distinguished by their quality derived from their totally handcrafted manufacturing process, which allows the helmets to be checked one by one by our experts, in each of the steps of the process. Thus detecting any possible fault in the construction. Only a few technicians can participate in the most complex parts of the process, and each one of them is specialized in his work.
Hand molded
Each shell is molded by hand. Our craftsmen's hands put together the best fibers and materials. Only a small group of experts, certified by our work standards, can take care of putting together the more than 20 materials needed to create the strongest possible helmet. And at every step of that process the shell is inspected for any imperfections that could compromise its integrity.
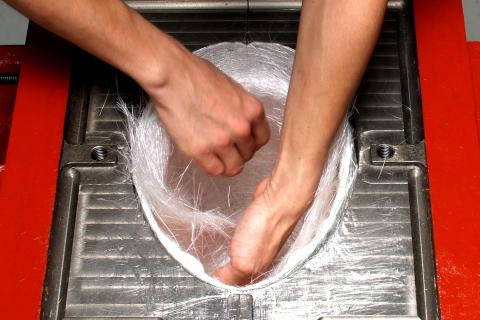
Technology and craftsmanship
Practically the entire process is done by hand. The only step that uses robotic processes is the cutting of the different openings in the shell. The different ventilation holes and the front opening for the visor are cut using a laser system to ensure a clean and precise cut on all helmets. In addition to that, the helmets are weighed and measured with precision micrometers in each part of the process, ensuring that Arai standards are met.
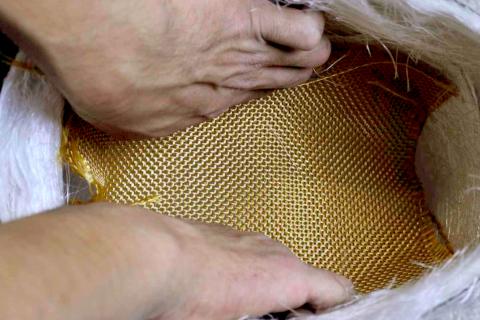
Process control
In addition to weighing, measuring and checking each shell after each part of the process, a firm control of all materials and processes is maintained. Each layer of material added is marked with the location and type of that material. The shell thickness is specified, the laser cuts are specified and, once checked and approved, each inspector must sign it and indicate its weight before it continues the manufacturing process of our Arai helmets.
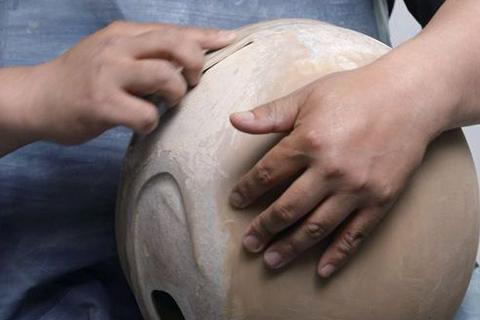
Polishing and priming
Arai helmets are built with the minimum amount of resin to limit the weight in their construction as much as possible, so their surface must be polished and filed before continuing with the process. After that, the helmets must be painted. This is a complex process in which several coats of primer are applied to the hull and polished several times. After several passes through the oven and a final wet polishing of the shell, the helmet has its first coat of paint. It is now ready for the complex process of applying the different designs.
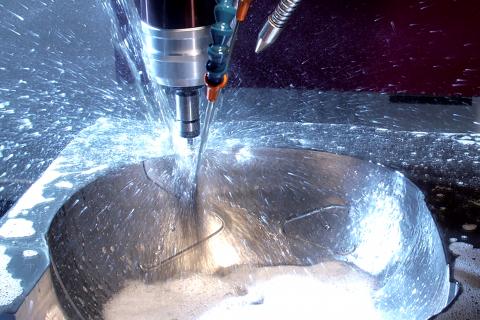
Embellecimiento
The shell is checked once again and prepared for beautification. It is here when the different paints or designs are applied by water transfer. The whole process is entirely manual and is strictly supervised for a perfect finish. The stencils are designed by hand and a different stencil is needed for each helmet size. After that the helmet is varnished and drilled to add the chin strap, ventilation and visor attachment. The bits must be replaced every few helmets due to the hardness of the Arai boots. Moldings are also added to the bottom and visor of the helmet.
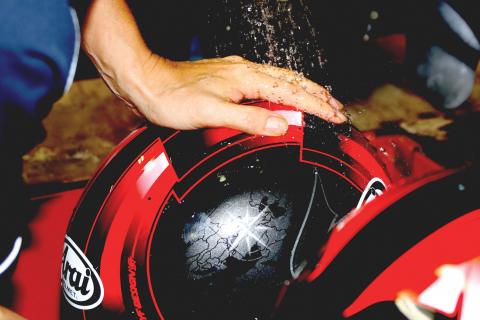
Interior
With the outer shell virtually complete, the inner EPS must be inserted. Only five people at the Arai factory are certified to perform this process due to its difficulty. The liner must be aligned perfectly so that the ventilation holes are perfectly aligned. Another important process is the installation of the chin straps. These are installed by hand and an independently performed inspection certifies the quality of their installation on such an important component.
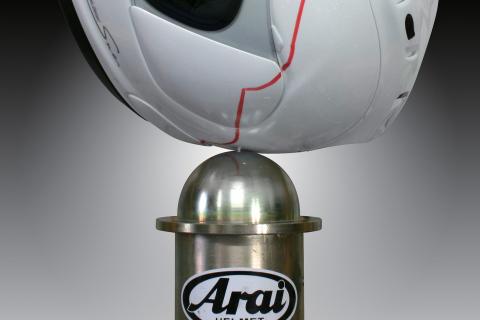
Visor and air intakes
Air intakes and other appendages are glued to the shell following precise templates using high-strength adhesives. They are specially designed to detach in the event of an accident so as not to affect the rebound capacity of the helmet and its impact deflection. Likewise, the visor is manually assembled and adjusted one by one to ensure proper installation and a tight fit. The helmet is almost ready, but first it must pass an exhaustive control with a long list of aspects to be taken into account. Once it has been checked, it is packed and shipped. And only two people are authorized to do this.
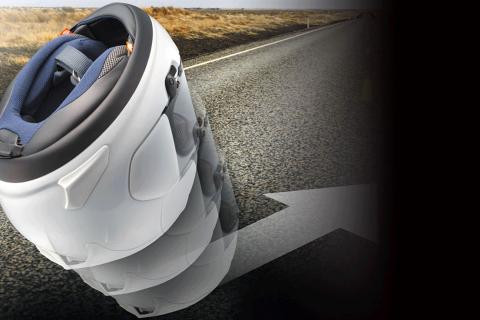